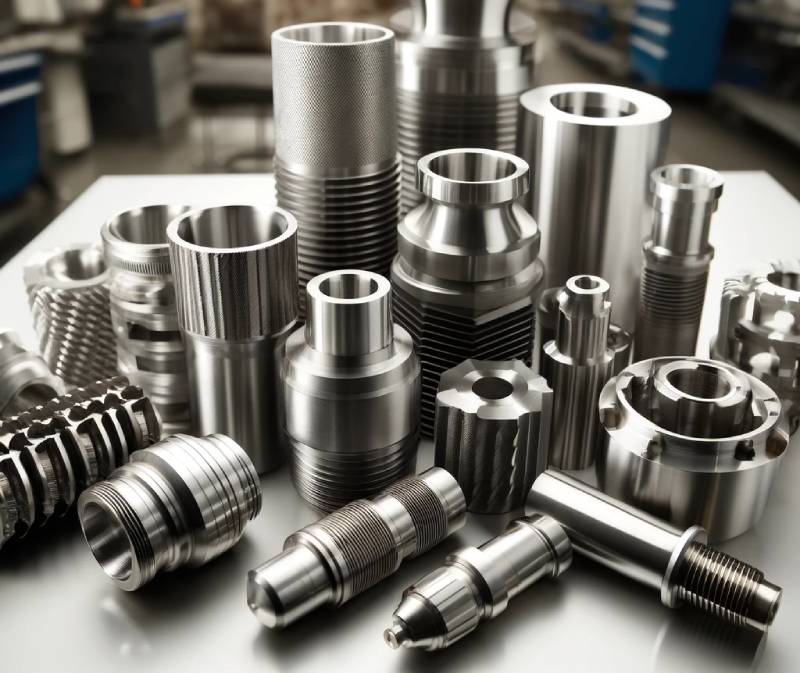
- Introduction
- Available Surface Finishes
- Available Surface Roughness
- Surface Finish Properties
- How to Select a Surface Finish for CNC Turned Parts
- Key Takeaways
- Komacut is Your One-Stop Solution
Table of Contents
CNC turning is a subtractive manufacturing process where a rotating workpiece is shaped by a stationary cutting tool which is controlled by a computer-controlled machine to fabricate CNC turned parts.
Introduction
When it comes to CNC machining, selecting the appropriate surface finish can be quite a challenge. With numerous finishing processes available, each with its strengths and weaknesses, finding the perfect match for specific applications can be overwhelming. Making the wrong choice can significantly impact part performance, resulting in reduced efficiency, compromised durability, or increased costs due to additional processing steps or unexpected wear.
A poor surface finish selection can lead to components that aren't fit for their intended purpose, causing issues like premature corrosion, insufficient heat resistance, or inadequate adherence to additional coatings. This can result in frequent part replacements, higher production costs, and even compromise the final product quality endangering your company’s reputation. Manufacturers who overlook these potential pitfalls might see a domino effect of costly delays and diminished market competitiveness.
That's where this comprehensive guide comes in. By breaking down the complexities of CNC surface finishes, we offer a clear path to your selection. You'll be able to make informed decisions that align with specific application needs, ensuring optimal performance and cost efficiency. Whether it's a matte finish to reduce glare or a polished surface to improve corrosion resistance, this guide will help you choose the right CNC surface finish.
Fig. 1: Surface Finishing Applied to CNC Turned Part
Available Surface Finishes
Surface finishes play a critical role in the quality, appearance, and performance of CNC turned parts. Depending on the application, different finishes can be applied to achieve desired characteristics, ranging from aesthetics to functionality. Here’s a detailed look at some of the most common surface finishes used in CNC machining:
Fig. 2: CNC Machined Parts at Komacut
- As-Machined Finish: This is the most basic finish, leaving the surface just as it was cut by the machine. Although it may show minor tool marks, it generally has a consistent appearance. This finish is often chosen for parts that don’t require a high degree of smoothness or visual refinement but emphasize functionality and cost-efficiency.
- Sand Blasting: This process involves propelling small particles of abrasive material onto the surface of the part to create a smooth, matte texture. It's suitable for parts that require a uniform, aesthetically pleasing finish with a matte look. However, it's not ideal for precision surfaces as it can round off edges.
- Anodizing: An electrochemical process that creates a protective oxide layer on the surface of aluminum and titanium parts, anodizing increases corrosion resistance and adds a decorative coating that can be dyed in various colors. Anodized finishes are especially popular in consumer products because they offer both aesthetics and durability.
- Powder Coating: Here, a dry powder is electrostatically applied to the surface before being cured in an oven, forming a tough and uniform coating. Powder coating is available in a wide range of colors and is highly durable, and resistant to impacts, scratches, and corrosion. It is suitable for parts that require both functional protection and attractive coloring.
- Electropolishing: This is a chemical process where parts are immersed in an electrolytic bath to remove a thin layer of material, thereby smoothing and brightening the surface. It's particularly useful for stainless steel components that require a highly polished, corrosion-resistant finish with a clean and sterile appearance.
- Brushed Finish: By using an abrasive belt or brush, this process creates a uniform pattern of fine lines across the surface. This gives the metal a satin-like sheen and is frequently used for decorative purposes, especially on visible parts like enclosures and consumer electronics.
- Passivation: Primarily for stainless steel, passivation uses acid baths to remove free iron and enhance the natural corrosion resistance of the material. This finish does not change the surface appearance but significantly improves the longevity of stainless steel parts in corrosive environments.
- Electroplating: Here, a thin layer of metal like gold, silver, or nickel is deposited onto the surface to enhance corrosion resistance, wear resistance, or electrical conductivity. Electroplating is often used in electronics and automotive parts that require enhanced functional characteristics.
Each of these surface finishes has its own merits and should be carefully considered based on application-specific requirements. Balancing cost, appearance, and performance will ensure the chosen finish aligns perfectly with the desired end product.
Available Surface Roughness
Surface roughness is a critical aspect of CNC machined parts, influencing factors such as friction, wear resistance, sealing performance, and overall aesthetics. It measures the small, finely spaced deviations on the part's surface, usually evaluated in Ra (Roughness Average). Let’s check into different roughness levels and their implications:
- Rough (Ra: 6.3 - 12.5 µm): This level is characteristic of an "as-machined" finish, where noticeable tool marks are visible on the surface. Such roughness may be suitable for applications where high friction is required or for internal components where aesthetics aren't a priority. However, the surface’s increased friction may hinder sealing and increase wear in dynamic components.
- Moderate (Ra: 3.2 - 6.3 µm): Often referred to as a fine or semi-finished surface, this level is achieved with secondary processing like milling or turning at lower speeds or with finer tools. While the surface retains some visible tool marks, it's smooth enough for parts where aesthetics are somewhat important, such as machinery components and automotive parts.
- Smooth (Ra: 0.8 - 3.2 µm): Commonly used in parts requiring moderate aesthetics or functionality, this roughness level is achieved through careful cutting or secondary operations like grinding. Smooth surfaces are important for reducing wear in moving parts or providing a better finish for painting or coating processes. It’s often seen in aerospace and precision engineering components.
- Very Smooth (Ra: 0.4 - 0.8 µm): At this level, the surface is almost mirror-like, typically achieved by precision grinding, honing, or lapping. It's perfect for high-precision components like bearings, hydraulic shafts, and other moving parts requiring low friction. The smoother surface provides excellent wear resistance and reduces the risk of contamination.
- Mirror-Like (Ra: 0.05 - 0.4 µm): Achieved through processes like lapping, polishing, or electropolishing, this ultra-smooth finish is reserved for applications where visual quality and minimal contamination risk are paramount. It is crucial for optical components, medical devices, and decorative parts requiring flawless aesthetics.
Surface roughness selection should match the intended function of the part. For example, if the part is subjected to constant movement or high wear, a smoother surface reduces friction and enhances longevity.
Conversely, in cases where adhesion or higher friction is desirable, such as in adhesive applications or structural bonding, a rougher surface may be more appropriate. Thus, the implications of surface roughness extend beyond aesthetics to profoundly impact the functionality and longevity of machined components.
Grade | Roughness (Ra) µm | Typical Applications |
---|---|---|
Very Rough | 12.5 - 25.0 | As-machined surfaces, heavy-duty machinery |
Rough | 6.3 - 12.5 | General-purpose machinery, parts -- coated or painted |
Moderate | 3.2 - 6.3 | Automotive parts, structural components |
Fine | 1.6 - 3.2 | Precision machinery, industrial equipment |
Very Fine | 0.8 - 1.6 | Aerospace components, high-end machinery |
Smooth | 0.4 - 0.8 | Bearings, hydraulic shafts, optical components |
Very Smooth | 0.2 - 0.4 | Medical devices, optics, and high-precision equipment |
Mirror-Like | 0.05 - 0.2 | Decorative finishes, precision lenses, medical implants |
Table 1: Surface Roughness Grades and Typical Applications
Surface Finish Properties
Surface finishes vary widely in their impact on mechanical properties, electrical conductivity, corrosion resistance, and cost. The selection of a suitable finish depends on balancing these factors with the intended application, ensuring optimal performance, longevity, and cost-efficiency.
Mechanical Properties
Surface finishes have significant implications on a part's mechanical strength and durability.
- For instance, sand blasting can produce a matte texture but might weaken mechanical properties due to abrasive surface alteration.
- Anodizing, on the other hand, enhances the hardness and wear resistance of aluminum parts through an oxide layer that increases surface strength.
- Electropolishing and passivation also improve mechanical properties by eliminating surface irregularities and enhancing material integrity, reducing fatigue points.
Electrical Conductivity
Surface finishes that influence electrical conductivity are crucial for electronic and electrical components.
- Electroplating with metals like gold or silver offers superior conductivity, ideal for electronic contacts.
- Nickel electroplating can also improve conductivity while providing corrosion resistance.
- Anodizing, however, generally reduces electrical conductivity due to the non-conductive oxide layer formed, making it unsuitable for conductive surfaces.
- For applications requiring electrical insulation, powder coating is effective, offering a thick, protective layer that prevents electrical contact.
Corrosion Resistance
Many surface finishes can dramatically enhance a part's resistance to corrosion.
- Anodizing creates a tough oxide layer that protects aluminum against oxidation and environmental wear.
- Passivation is particularly useful for stainless steel, removing free iron and forming a passive layer resistant to rust and chemicals.
- Powder coating forms a dense, impact-resistant barrier to moisture and corrosion.
- Electropolishing reduces surface irregularities, thus minimizing corrosion sites and contamination buildup.
Cost
When considering cost-effectiveness, as-machined finishes are the least expensive, and suitable for internal components where aesthetics or precision are not paramount.
- Sand blasting provides a cost-effective improvement in aesthetics and uniformity.
- Anodizing, though more costly, remains a popular choice due to its durability and aesthetic appeal.
- Powder coating and electroplating require more specialized equipment and preparation, increasing costs but delivering a high-quality finish.
- Electropolishing and passivation are comparatively expensive but are justified in critical applications where hygiene and corrosion resistance are vital.
How to Select a Surface Finish for CNC Turned Parts
Selecting the appropriate surface finish for CNC turned parts requires carefully balancing the functional, aesthetic, and economic aspects of the part's intended use.
Here's a guide for choosing finishes based on application needs, as well as specific recommendations for gears, bushings, and other commonly machined components.
Fig. 3: CNC Turned Part
Application Needs
When determining which surface finish to apply, consider the operational requirements of the part. For example, does it need to resist corrosion in a harsh environment, reduce friction in moving assemblies, or require a specific aesthetic appeal?
- Corrosion Resistance: Choose anodizing, passivation, or powder coating if the component will operate in a corrosive environment or come in contact with moisture or chemicals.
- Friction Reduction: Electropolishing and precision grinding produce smooth surfaces that minimize friction, essential for moving parts like bearings or sliding shafts.
- Wear Resistance: many applications where there is part on part movement will require a certain level of abrasion or wear resistance, so that the surface finish can hold up to friction and not peel or degrade. This is especially true for applications with long lifetime expectations
- Electrical Insulation/Conductivity: Powder coating provides electrical insulation while electroplating with metals like gold or nickel offers high conductivity.
- Aesthetic Appeal: Consider anodizing, powder coating, or sand blasting for parts with prominent visual exposure.
- Weather & UV Resistance: for outdoor applications, it’s important to consider whether the surface finish can hold up to extended exposure to sun, dirt, and other conditions.
Finish | Corrosion Resistance | Aesthetic Appeal | Friction Reduction | Wear Resistance | Electrical Insulation/Conductivity | Weather & UV Resistance |
---|---|---|---|---|---|---|
Anodizing | High | High | Low | Medium | Low | Medium |
Passivation | High | Low | Low | Low | Low | Low |
Powder Coating | High | High | Low | Medium | High (Insulation) | High |
Electropolishing | Low | Medium | High | Medium | Low | Low |
Precision Grinding | Low | Low | High | High | Low | Low |
Electroplating (Gold/Nickel) | Low | Medium | Low | Medium | High (Conductivity) | Low |
Sand Blasting | Low | High | Low | Low | Low | Medium |
Table 2: Comparative Analysis of Surface Finishes
Part-Specific Needs
Different CNC turned parts have specific requirements due to their unique roles and environments. Here are some common CNC turned parts requirements:
Gears
Gears require surface finishes that enhance performance, minimize wear, and reduce noise.
- Precision grinding or honing is often used to provide a smooth, accurate profile that ensures consistent meshing.
- For gears in corrosive environments, electropolishing is advantageous for removing surface defects and improving wear resistance
- nickel plating can offer additional hardness and corrosion resistance.
Bushings
Bushings are subject to high wear and require finishes that minimize friction and ensure a long lifespan.
- Electropolishing provides a smooth surface that helps reduce friction and prevents contaminants from adhering to the surface.
- Anodizing can offer extra hardness and wear resistance for aluminum bushings,
- passivation is beneficial for stainless steel variants [what does this have to do with bushing?]
- Bushings will generally have tight tolerances requiring surface finishes with minimal variation in thickness, such as anodization or plating processes.
Shafts
Shafts require finishes that balance wear resistance and friction reduction.
- Fine grinding and electropolishing create surfaces that minimize friction and extend lifespan.
- In cases where corrosion resistance is critical, anodizing or passivation may be beneficial.
- Shafts with tight tolerances require surface finishes with minimal variation in thickness, such as hard anodization or plating processes.
- Finishes which abrade easily like powder coating or electroplating should NOT be used.
Fasteners and Screws
- Electroplating with zinc, nickel, or other metals protects fasteners from corrosion while enhancing their appearance.
- For fasteners exposed to corrosive environments, electropolishing or passivation ensures optimal durability.
- Geomet offers some of the most complete corrosion protection for fasteners from corrosion, which is why it is often selected for automotive applications.
Valve Components
Valves demand tight tolerances and smooth surfaces to prevent leaks and ensure efficient operation.
- Precision grinding or honing creates surfaces that minimize friction and reduce contamination.
- Tight tolerances require surface finishes with minimal variation in thickness, such as electroplating or anodizing.
- Finishes which abrade easily like powder coating should NOT be used.
Enclosures
- Sand blasting and powder coating are often chosen for enclosures to provide a consistent, attractive finish that resists corrosion.
- Anodizing can offer a high-quality, durable coating for aluminum enclosures.
Selecting the right surface finish for CNC turned parts is crucial for achieving optimal performance, durability, and appearance. By understanding the operational requirements and unique needs of each part, you can make an informed decision that aligns with specific functional goals while balancing cost and efficiency.
Part Type | Anodization | Powder Coating | Plating | Sand Blasting | Electropolishing | Precision Grinding | Geomet Coating |
---|---|---|---|---|---|---|---|
Gears | Not typically used | Not typically used | Nickel plating for hardness and corrosion resistance | Not typically used | For removing surface defects and improving wear resistance | For smooth, accurate profiles ensuring consistent meshing | Not typically used |
Bushings | Extra hardness and wear resistance (for aluminum) | Not typically used | Electropolishing for smoothness; Passivation for stainless steel | Not typically used | Provides a smooth surface to reduce friction | Not typically used | Not typically used |
Shafts | For corrosion resistance and minimal thickness variation | Not suitable | Not suitable | Not typically used | Creates surfaces that minimize friction | For creating surfaces that extend lifespan | Not typically used |
Fasteners/Screws | Not typically used | Not typically used | Zinc, Nickel for corrosion protection | Not typically used | For durability in corrosive environments | Not typically used | Provides complete corrosion protection, often used in automotive applications |
Valve Components | For minimal thickness variation | Not suitable | Electroplating for tight tolerances | Not suitable | For minimizing friction and reducing contamination | For creating surfaces that minimize friction | Not typically used |
Enclosures | High-quality, durable coating for aluminum | Consistent, attractive finish that resists corrosion | Not typically used | Consistent, attractive finish that resists corrosion | Not typically used | Not typically used | Not typically used |
Table 3: Surface Treatment Suitability for Different Part Types
Key Takeaways
Different finishes—such as anodizing, powder coating, electropolishing, and passivation—offer unique mechanical, electrical, and protective properties to address varying operational requirements. Understanding the nuances of surface roughness levels, from "as-machined" to "mirror-like," can help ensure that each part meets its functional needs efficiently.
For gears, a precise finish reduces noise and wear, while for bushings, it prolongs lifespan by minimizing friction. Similarly, specialized finishes like electroplating for fasteners or grinding for valve components provide critical enhancements tailored to specific operational demands. Ultimately, choosing the right finish means achieving higher performance, reducing maintenance costs, and optimizing overall product value.
Komacut
Enhancing your CNC turned parts with the ideal surface finish is not just a choice—it's an investment in quality and reliability. Visit Komacut website to explore a wide array of options for CNC surface finishes. With an advanced online quotation engine, precision manufacturing is at your fingertips. Take the next step towards superior manufacturing by harnessing the power of tailored surface finishes, and discover how Komacut can help you deliver excellence in every part you produce.