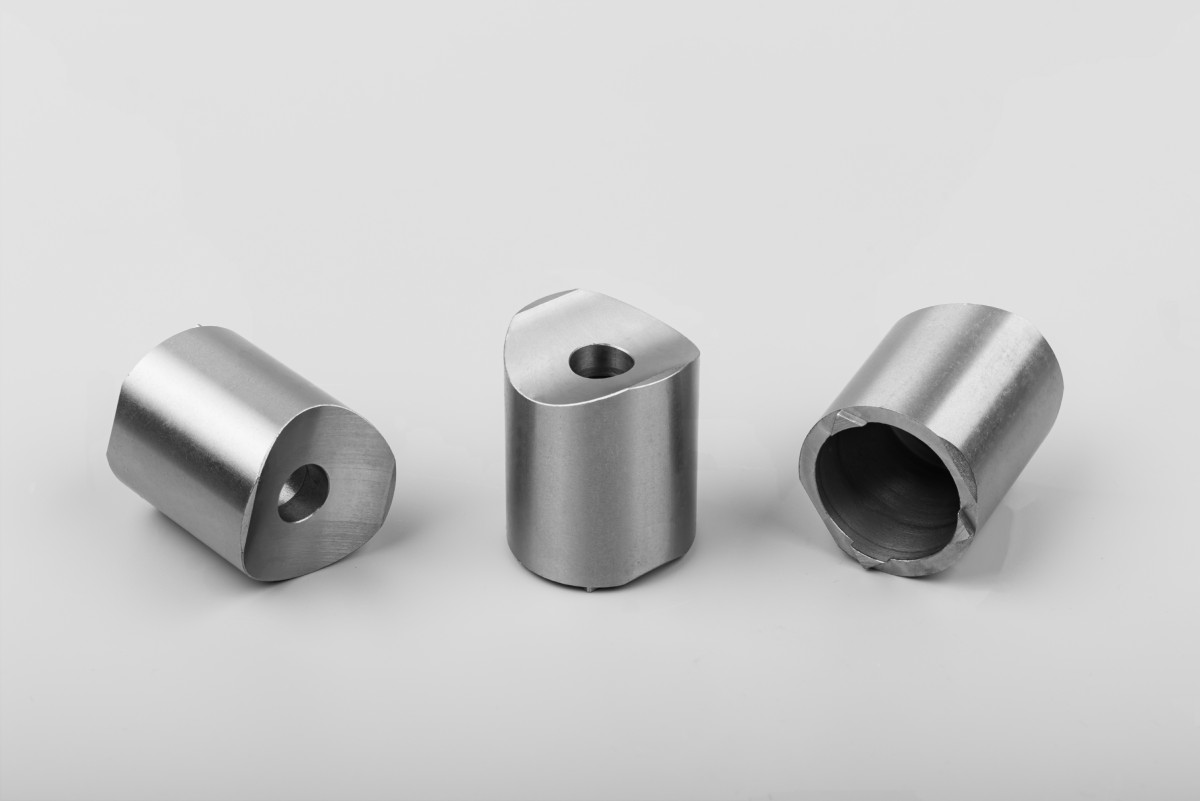
- Introduction
- What is CNC Turning
- What Kind of Parts Are Made by CNC Turning?
- Types of Parts Made by CNC Turning
- How to Determine Which Parts Are Best Made by CNC Turning
- The Komacut Advantage
- FAQs
CNC turning excels at producing cylindrical or axially symmetrical parts with precision and efficiency. Common parts manufactured using CNC turning include shafts, pins, bushings, and connectors. Its capability to efficiently machine rotational features, such as threads, grooves, and tapers, makes it ideal for a wide range of applications across industries.
Table of Contents
Introduction
CNC machining, short for Computer Numerical Control machining, is a manufacturing process where computer-controlled machines accurately and efficiently shape raw materials into finished parts. Utilizing precise instructions programmed into the machine via computer-aided design (CAD) software, CNC machining enables the automated control of cutting tools and workpiece positioning. It enables the production of highly intricate and precise parts across a wide range of materials, from metals to plastics, with speed, consistency, and repeatability.
Fig. 1: CNC Turned Parts
The CNC turning process involves securing the raw material onto the lathe, where it is rotated while a single-point cutting tool moves parallel to the axis of rotation, shaping the material accordingly. Precise measurements are input into the machine through CAD software. The computer controls the lathe to ensure the manufactured parts meet the exact specifications required.
Fig. 2: CNC Turning Process
What Kind of Parts Are Made by CNC Turning?
- Symmetrical – you can have parts with asymmetrical features, but the overall part shape will need to be symmetrical. This has to do with the spinning of the work piece and the stationary position of the part
- Cylindrical or round – again, due to the processes’ nature, cylindrical or round parts are what is best suited for CNC turning.
- Can be produced from bar or tube stock – the process is working from solid bars of raw material, or tubes. The inner and outer diameter are then shaped by the work piece. If the part is too big or too small, there may not be suitable material for working.
Types of Parts Made by CNC Turning
CNC turning is versatile and well-suited for producing a wide range of components having features symmetrical around a central axis. Here's a table categorizing parts that can be made by CNC turning across various industries:
Industry | Parts Made by CNC Turning |
---|---|
Aerospace | Shafts, pins, spacers, bushings, hydraulic fittings |
Automotive | Axles, drive shafts, camshafts, crankshafts, pulleys |
Medical | Surgical instruments, bone screws, dental implants |
Electronics | Connectors, terminals, contact pins, housings |
Oil & Gas | Valves, fittings, couplings, hydraulic components |
Marine | Propeller shafts, couplings, marine engine components |
Defense | Gun barrels, ammunition casings, ordinance components |
Construction | Nuts, bolts, screws, fasteners, hinges |
Consumer Goods | Door handles, knobs, faucet components, tool handles |
Energy | Turbine shafts, rotors, generator components |
Industrial | Bearings, gears, pulleys, couplings |
Table 1: CNC Turning Applications Across Various Industries
These are the broad range of components that can be efficiently manufactured using CNC turning, demonstrating its versatility and effectiveness in meeting diverse industrial needs:
- Bushings: These cylindrical components are utilized to reduce friction between two surfaces and maintain alignment in mechanical assemblies. They are made with uniform dimensions and smooth surfaces essential for optimal bushing performance.
- Rings: Whether used for sealing, bearings, or decorative purposes, rings demand precise circular dimensions and smooth finishes, making CNC turning an ideal method for crafting them efficiently.
- Flanges: These are essential parts for connecting pipes, valves, and other equipment in piping systems, flanges require precise circular shapes with accurately positioned bolt holes.
- Pins and Dowels: These cylindrical components serve various functions, such as aligning parts, providing support, or acting as pivot points. They must have accurate dimensions and smooth surfaces necessary for their intended applications.
- Spacers: Often used to maintain specific distances between components or to fill gaps, spacers require precise outer diameters and lengths.
- Pulleys: Found in systems like conveyors, engines, and transmissions, pulleys transmit rotational motion and require precise grooves or teeth profiles. They need to be accurately machined to ensure smooth operation.
Fig. 3: CNC Turned Bushings
- Cylindrical Joints: Parts such as couplings, couplers, and adapters often require cylindrical geometry to facilitate the connection between different components. They need to have precise dimensions and concentricity needed for reliable joint performance.
- Couplings: These components connect two shafts for transmitting power or motion. They must have precise outer diameters, bore sizes, and keyways to achieve proper alignment and torque transmission.
- Bolts and Fasteners: Fasteners such as bolts, screws, and studs require precise threads and shank diameters to securely join components together. Especially when non-standard sizes or smaller quantities are needed, these parts can be produced from forged blanks with the appropriate head size and overall diameter, and then CNC turning is used to create consistent thread profiles and tight tolerances.
- Hubs: Found in wheels, gears, and pulleys, hubs provide a central connection point for attaching other components. CNC turning can create hubs with accurate diameters, bores, and keyways for proper alignment and assembly.
- Rollers: Used in conveyors, printers, and industrial machinery, rollers require precise cylindrical surfaces for smooth rotation and material handling. They must have the necessary dimensional accuracy and surface finish for optimal performance.
- Axles: Axles transmit rotational motion between rotating components such as wheels, gears, or pulleys. Axles must have precise diameters, shoulders, and keyways to ensure proper fit and alignment within assemblies.
- Nozzles: Found in various applications such as fluid dispensing systems or spray equipment, nozzles require precise internal and external geometries for controlled fluid flow. Nozzles need to have accurately machined bores, tapers, and outlet profiles to meet specific performance requirements.
Fig 4: CNC Turned Couplings
- Shafts: Commonly used in machinery to transmit power or rotational motion, shafts require precise cylindrical shapes and often feature keyways or threads, which can be accurately produced using CNC turning.
- Housings: Housings are cylindrical enclosures used in various applications such as firearms, machinery, or automotive components. Barrel housings should have precise bore diameters, thread patterns, and mounting features for assembly and functionality.
- Stems: Stems are structural components used in applications such as valves, faucets, or medical devices. CNC turning can produce stems with accurate diameters, threads, and sealing surfaces to ensure proper functionality.
Fig. 5: Precision CNC Turned Metal Components
How to Determine Which Parts Are Best Made by CNC Turning
Symmetry and Geometry - CNC turning is particularly advantageous for parts with symmetrical geometries due to its rotational nature. Parts with rotational symmetry, such as shafts, cylinders, and discs, are ideally suited for CNC turning to ensure uniformity and precision.
Cylindrical & Round Shapes - Turned parts are inherently cylindrical or round, and either solid or hollow, primarily due to the nature of the turning process. This cylindrical form is well-suited for a wide range of applications across various industries, including automotive, aerospace, and manufacturing. Solid cylindrical parts, such as shafts and pins, provide structural support and transmit motion or power efficiently. Hollow cylindrical parts, like tubes and sleeves, offer lightweight construction and fluid passage capabilities.
Material Starting Form - CNC turning is especially suited for parts that can begin as bar stock or other cylindrical preforms. This starting form minimizes material waste and simplifies the machining process, as the cylindrical shape of the workpiece aligns naturally with the rotational motion of the lathe. Bar stock, typically available in various diameters and lengths, provides a cost-effective and readily available starting material for turned parts.
Complexity and Features - Despite its association with cylindrical shapes, CNC turning can efficiently produce parts with a wide range of complex features. Multi-axis machining and live tooling capabilities, enable the incorporation of intricate geometries such as threads, grooves, and chamfers directly during the turning process. Threads, essential for fasteners and fittings, can be accurately cut using specialized threading tools, ensuring precise pitch and depth control. Grooves, used for O-ring seats or decorative purposes, can be machined with high repeatability and surface finish using custom tooling configurations.
Material Compatibility - CNC turning is well-suited for machining a wide range of materials, including metals, plastics, and composites. It is particularly effective for softer materials like aluminum, brass, and plastics, as well as certain stainless steel and alloys. These materials exhibit favorable machinability characteristics when subjected to the cutting forces and temperatures generated during turning operations. CNC turning can achieve high-quality surface finishes and dimensional accuracy on these materials, making it an ideal choice for parts requiring excellent aesthetics or tight tolerances.
Production Volume and Efficiency - The production volume of the parts can influence the decision to use CNC turning. While CNC milling may offer advantages for low-volume or prototype production due to its versatility and ability to handle complex geometries, CNC turning excels in high-volume production requirements. The rotational nature of turning allows for continuous and rapid machining of cylindrical parts, resulting in shorter cycle times and increased throughput compared to milling.
Tooling and Setup Requirements - CNC turning typically requires minimal tooling and setup compared to other machining processes, making it suitable for quick turnaround times and rapid production ramp-up. The primary tooling components in turning include cutting inserts, tool holders, and work-holding fixtures, which are relatively straightforward to set up and replace as needed. The simplicity of the turning process also reduces the risk of tool breakage or machine downtime, ensuring consistent and uninterrupted production.
Secondary Operations Integration - CNC turning allows for seamless integration of secondary operations such as drilling, tapping, and knurling within the same machining cycle. This capability eliminates the need for additional setups or transfers to secondary machines, reducing production lead times and costs. For example, tapped holes can be accurately machined directly on turned parts using live tooling attachments, ensuring precise thread alignment and dimensional accuracy.
Surface Finish Requirements - CNC turning can achieve excellent surface finishes on cylindrical and contoured surfaces, meeting the stringent requirements of various applications such as automotive, aerospace, and medical devices. The cutting tools used in turning generate consistent cutting forces and chip formation patterns, resulting in smooth and uniform surface textures.
Cost Considerations - When evaluating the suitability of CNC turning for specific parts, it's essential to consider cost factors such as material expenses, machine utilization rates, and labor requirements. CNC turning offers competitive pricing advantages for parts that align with its strengths, such as cylindrical geometries, high-volume production, and minimal setup complexity. By optimizing tooling strategies, minimizing material waste, and maximizing machine uptime, manufacturers can leverage CNC turning to achieve cost-effective production solutions without compromising on part quality or performance.
The Komacut Advantage
Are you in need of precision CNC turning services for your next project? Look no further than Komacut. With our extensive expertise in creating CNC turned and machined parts, as well as our modern facilities, instant quoting and large technical team, whether you require simple cylindrical components or complex geometries, we have the capabilities and experience to meet your exact specifications.
At Komacut, we understand the importance of delivering high-quality parts on time and within budget. Our team of skilled machinists and engineers is dedicated to providing superior craftsmanship and attention to detail in every project we undertake.
Don't settle for anything less than the best when it comes to CNC turning. Get a true instant quote online for up to 100k parts, in different materials and with different surface finishes in seconds, or reach out to discuss your project requirements and discover how we can help bring your vision to life with precision and reliability. Let us be your trusted partner in machining excellence.
FAQs
What materials can be used in CNC turning?
CNC turning can accommodate a wide range of materials, including metals, plastics, and composites. Common materials used in CNC turning include aluminum, brass, stainless steel, carbon steel, titanium, copper, and various engineering plastics such as nylon, acetal, and polycarbonate. CNC turning can also machine specialty materials like ceramics, fiberglass, and certain types of wood, depending on their machinability characteristics and application requirements.
How does CNC turning compare to CNC milling?
CNC turning and CNC milling are both subtractive manufacturing processes that use computer numerical control (CNC) machines to shape workpieces into finished parts. The key difference lies in how the cutting tool and workpiece interact: in CNC turning, the workpiece rotates while the cutting tool remains stationary, whereas in CNC milling, the cutting tool rotates while the workpiece remains stationary.
Can CNC turning produce parts with non-cylindrical features?
While CNC turning is commonly associated with cylindrical parts due to its rotational nature, it can also produce parts with non-cylindrical features using advanced machining techniques and tooling configurations. For example, CNC turning machines equipped with live tooling capabilities can perform secondary operations such as drilling, milling, and threading during the turning process, enabling the creation of complex geometries like grooves, slots, and angled surfaces.
What are the tolerances achievable with CNC turning?
CNC turning can achieve tight tolerances and high precision, making it suitable for applications that demand dimensional accuracy and consistency. CNC turning can achieve tolerances ranging from ±0.001 to ±0.005 inches (±0.025 to ±0.127 millimeters) for most metals and plastics. However, tighter tolerances down to ±0.0005 inches (±0.013 millimeters) or even better can be achieved with careful process optimization, precision tooling, and advanced machining techniques.
What are the advantages of CNC turning over traditional manual turning?
CNC turning machines can operate continuously, 24/7, without the need for operator intervention, leading to higher productivity and reduced labor costs. CNC turning offers increased efficiency, repeatability, and versatility compared to traditional manual turning techniques.
How does CNC turning contribute to reducing material waste and increasing material utilization?
CNC turning machines can precisely control cutting depths and tool paths, minimizing excess material removal and maximizing part yield from raw material stock. CNC turning allows for efficient nesting and clustering of parts on the workpiece, reducing scrap and maximizing material usage per machining cycle.
How does CNC turning accommodate parts with varying complexity levels?
For less complex parts, CNC turning can efficiently produce features such as outer diameters, inner bores, and facing operations using standard turning tooling and techniques. For more complex parts requiring additional features or secondary operations, CNC turning machines equipped with live tooling, sub-spindles, and multi-axis capabilities can perform drilling, milling, tapping, and thread-cutting operations directly on the turning center.
What considerations should be made when selecting cutting tools for CNC turning?
Tool material and coating selection should be based on the workpiece material being machined, with carbide, cermet, and high-speed steel being common options. Additionally, tool geometry, including rake angle, clearance angle, and chip breaker design, should be chosen to match the specific machining application and material properties. Cutting tool inserts with high wear resistance and thermal stability can prolong tool life and reduce machining costs.