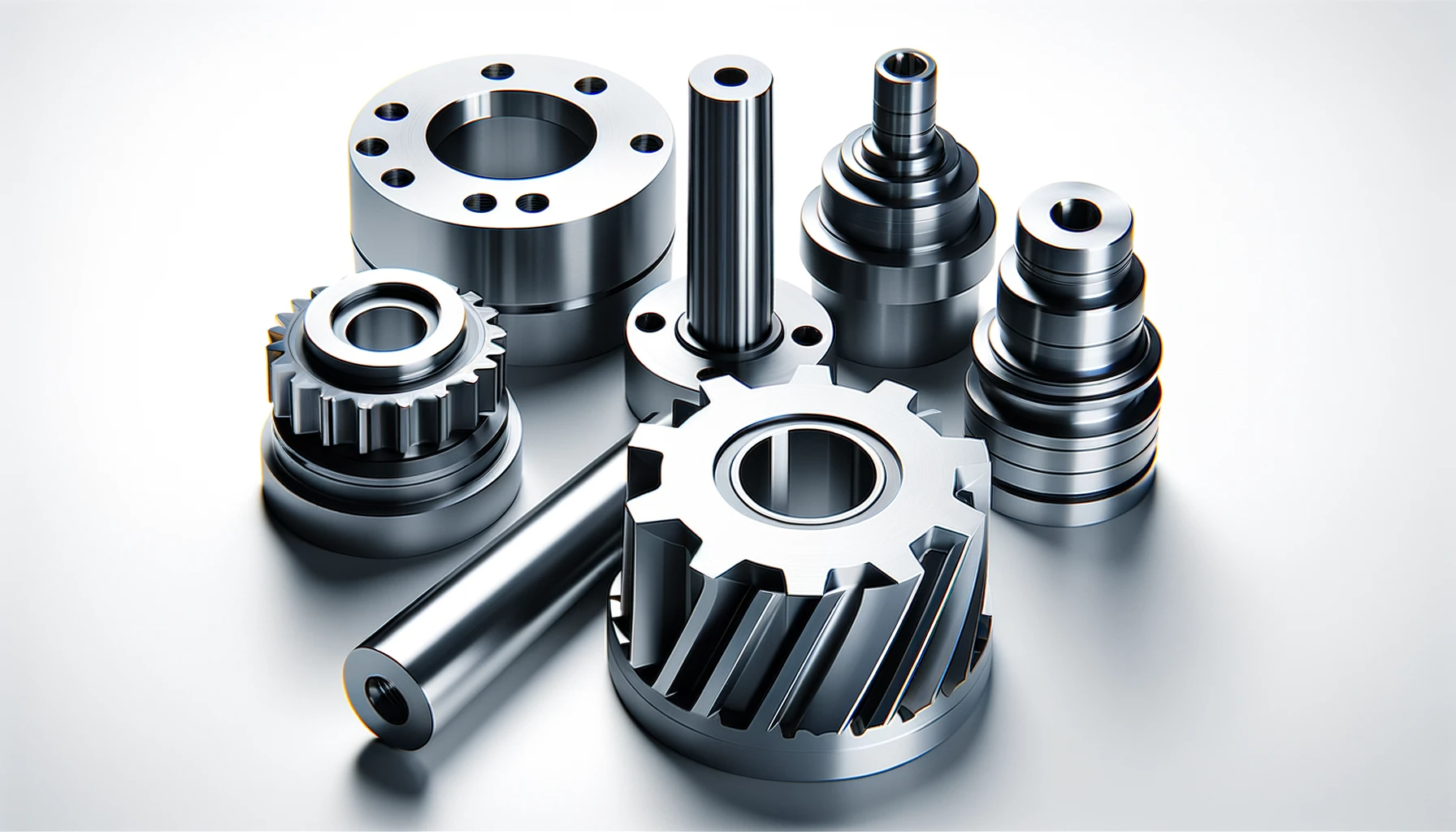
- What is CNC Surface Roughness?
- What Are Typical Surface Roughnesses for CNC Machining?
- Explanation of the Different Surface Roughnesses
- Which Surface Roughness to Select?
- How to Measure of Surface Roughness
- Conclusion
- FAQs
Surface roughness describes the micro-level texture of a surface created during CNC machining which is characterized by tiny peaks and valleys. It's quantified using measurements such as the average roughness (Ra), which indicates the average deviations from the surface's mean line.
Table of Contents
What is CNC Surface Roughness?
CNC (Computer Numerical Control) machining is a highly precise and automated manufacturing process that uses computerized controls and machine tools to remove layers of material from a workpiece, thereby shaping it into a desired design. CNC machining includes both CNC milling and CNC turning.
CNC surface roughness is the measure of the texture of a surface created during that machining process, characterized by the size of irregularities and ridges on the surface of the machined part. These surface features, often microscopic, are the result of the cutting action of the tool on the material's surface and are inherent to the manufacturing process.
Surface roughness is a critical quality attribute, influencing not only the aesthetic appearance of the part but also its functional performance, including wear resistance, fatigue strength, and lubrication capabilities. Several metrics are employed to quantify surface roughness, among which Rₐ (average roughness) and Rz (maximum height of the roughness profile) are the most common.
- Rₐ represents the average deviation of the roughness irregularities from the mean line of the surface over a specified length. It provides a statistical average value that reflects the general texture of the surface but does not capture extreme values or peaks and valleys.
- Rz, on the other hand, measures the vertical distance between the highest peak and the deepest valley within a given length of the surface.
- Lay refers to the predominant direction of the surface texture. It affects properties like friction and wear, with different patterns performing uniquely in various applications.
Fig. 1: Surface Roughness Concepts: Rₐ, Rz and Lay
What Are Typical Surface Roughnesses for CNC Machining?
Manufacturers often offer four surface roughness levels that are typically specified for CNC Machining applications:
3.2 μm Rₐ
- This is the standard commercial machine finish. It is suitable for most consumer parts and sufficiently smooth, but it contains visible cut marks. It is the default surface roughness applied unless otherwise specified.
- 2 μm Ra is the recommended maximum surface roughness for parts subject to stress, loads, and vibrations.
- It can also be used for mating moving surfaces when the load is light and the motion is slow.
- Processing - It is machined using high speeds, fine feeds, and light cuts.
- Price – this is the baseline finish for parts, zero additional cost.
1.6 μm Rₐ
- Usually, there are only slightly visible cut marks with this option.
- This Rₐ rating is recommended for tight fits and stressed parts and is sufficient for slow-moving and light load-bearing surfaces.
- It is not suitable for fast-rotating parts and parts subject to intense vibration.
- Processing - This surface roughness is produced using high speeds, fine feeds, and light cuts under controlled conditions.
- For a standard aluminum alloy (e.g. 3.1645) this option adds approximately 2.5% to the production price. This could increase with the complexity of the part.
0.8 μm Rₐ
- Considered high grade, this surface finish requires very close control to produce, costing more.
- This finish is required for parts that are exposed to stress concentration. When the motion is occasional and the loads are light, then it can be used for bearings.
- Price- for a standard aluminum alloy (e.g. 3.1645) this option adds approximately 5% to the production price. This could increase with the complexity of the part.
0.4 μm Rₐ
- This is the finest (“least rough” in technical terms) and highest quality surface roughness that is offered.
- It is suitable for parts that are under high tension or stress. It is also required for rapidly rotating components such as bearings and shafts.
- This surface roughness takes the most effort to manufacture and should only be specified when smoothness is of primary importance.
- Price- for a standard aluminum alloy (e.g. 3.1645) this option adds approximately 11-15% to the production price. This could increase with the complexity of the part.
Surface Roughness Level | Characteristics | Recommended Applications | Processing | Price Impact |
---|---|---|---|---|
3.2 μm Rₐ |
|
|
|
|
1.6 μm Rₐ |
|
|
|
|
0.8 μm Rₐ |
|
|
|
|
0.4 μm Rₐ |
|
|
|
|
Table 1: CNC Machining Surface Roughness Levels
Explanation of the Different Surface Roughnesses
The spectrum of surface roughness in CNC machined parts ranges from very smooth to very rough, each serving distinct practical purposes and influencing the part's application and performance. This spectrum can be visualized and quantified using surface roughness charts or online tools that categorize surface finishes by their Ra values (average roughness) in micrometers or micro inches.
At the very smooth end of the spectrum, surfaces with extremely low Ra values, typically less than 0.4 µm (16 µin), are achieved through processes like fine grinding, lapping, or polishing. These ultra-smooth surfaces are essential for applications requiring minimal friction, high precision, or aesthetic qualities. Examples include sealing surfaces, optical components, and parts that come into contact with fluids, where any irregularity could lead to leakage or flow disruption.
Surfaces with Ra values between 0.4 µm (16 µin) and 1.6 µm (63 µin) are considered smooth but not glossy. These finishes are common for parts that require good functional performance without the need for an ultra-smooth finish. Such surfaces are adequate for many general engineering applications where moderate contact and wear resistance are needed, including various components in machinery and automotive parts.
Ra values from 1.6 µm (63 µin) to 6.3 µm (250 µin) are categorized as medium surface roughness. These finishes are typical for parts that do not require high precision in terms of surface contact but need to be durable and cost-effective. This roughness level is common in structural components, parts that require coating or paint, and where the surface finish is not critical to the part's performance.
At the rough end of the spectrum, with Ra values above 6.3 µm (250 µin), surfaces are considered very rough. These finishes are often the result of basic machining processes, such as milling or turning, without any post-processing to reduce the surface roughness. Parts with such rough finishes are used in applications where the surface finish has little to no impact on the part's functionality.
Roughness | Stainless Steel | Carbon Steel | Aluminium |
---|---|---|---|
As Milled ≤ 6.0 μm Ra | |||
Standard ≤ 3.2 µm Ra | |||
Fine ≤ 1.6 µm Ra | |||
High Grade ≤ 0.8 µm Ra |
Fig. 2: Komacut's Guidelines on Surface Roughness for CNC Turning
Which Surface Roughness to Select?
Selecting the appropriate surface roughness for CNC machined parts is a crucial decision that hinges on balancing technical requirements with cost considerations. In practical terms, the choice of surface roughness will significantly influence both the functionality and the cost-effectiveness of the part.
Is it a Moving Part?
In applications involving moving parts, especially those operating at high RPMs, a lower level of surface roughness is essential. This smoother finish reduces friction, thereby enhancing the part's efficiency and lifespan by minimizing wear and energy consumption. Such precision, while increasing production costs due to more stringent machining and finishing requirements, is necessary for ensuring optimal performance and reliability of critical components.
For parts where movement is not a concern, such as a simple pin that needs to be positioned into place, a less fine surface finish, like a milled finish, may suffice. This approach can significantly reduce manufacturing costs as it involves fewer processing steps and less precise equipment. Here, the technical demands do not justify the higher costs associated with finer finishes, making a rougher surface an economical choice without compromising the part's functional integrity.
Is it an Aesthetic Part?
The choice between aesthetic and non-aesthetic parts also plays a role in determining the suitable surface roughness. Aesthetic components, often visible in the final product, require a smoother finish to enhance visual appeal and tactile quality, reflecting the product's overall quality. This is crucial in consumer-facing parts, such as electronics or automotive interiors, where the consumer's perception can directly impact the brand's reputation and product desirability.
In contrast, parts typically hidden from view can tolerate higher roughness levels, focusing purely on functional requirements rather than appearance. Thus, understanding the part's application, the material used, and end-use requirements is fundamental in making an informed decision about surface roughness, balancing performance, aesthetics, and cost-effectiveness.
Other Factors
Surface roughness also has an impact on several other factors in part function, everything from electrical conductivity to how easy the part is to sanitize or clean. We’ve created a simple table to provide an overview of how different levels of surface roughness impact various aspects of CNC machined parts.
Impact on | Reason | Roughness | Ra (µm) |
---|---|---|---|
Cost | Finer surface finishes require more intricate machining and additional post-processing like grinding, lapping, or polishing, which are more costly due to the equipment and slower speeds. | Finer | 0.1 to 0.4 |
Part-on-Part Contact | A smoother finish improves alignment and reduces friction, enhancing efficiency, whereas a rougher finish may increase wear but helps retain lubricants. | Varied Roughness | Smoother: <0.8, Rougher: >1.6 |
Tolerances | Tight tolerances enhance the visual cohesiveness and reliability of components, affecting assembly precision and brand reputation. | Smoother | 0.1 to 0.4 |
Appearance | Surface roughness impacts visual and tactile qualities, influencing consumer perception and product appeal. | Smoother | <0.8 |
Electrical Conductivity | Smoother surfaces provide better contact points in electrical connectors, improving conductivity and component performance. | Smoother | <0.8 |
Hygiene and Cleanability | Smoother surfaces are easier to clean and sterilize, reducing contamination risks in sensitive environments like medical and food processing. | Smoother | <0.8 |
Lubrication Retention | Roughness can create micro-pockets that trap lubricants, enhancing lubrication effectiveness and reducing wear in moving systems. | Rougher | >1.6 |
Sealing and Leakage Prevention | Smoother surfaces ensure tighter contact in seals, reducing leakage in systems such as hydraulics and pneumatics. | Smoother | <0.8 |
Coating and Paint Adhesion | A certain level of roughness increases the surface area for adhesion, improving the durability and longevity of paints and coatings. | Rougher | 1.6 to 6.3 |
Optical Properties | The level of roughness affects how light is reflected, refracted, and transmitted, impacting the performance of optical components. | Smoother | <0.1 |
Table 2: Impact of Surface Roughness on Various Factors
How to Measure of Surface Roughness
These roughness parameters are typically measured using specialized instruments, such as profilometers, which can either be contact-based, dragging a stylus across the surface to measure variations in height, or non-contact, using optical or laser scanning technologies to map the surface's topology.
Fig. 2: Profilometer
The choice of measurement technique depends on the required accuracy, the nature of the machined surface, and the specific application of the part. Understanding and controlling surface roughness through these metrics is essential for optimizing the functional performance and longevity of CNC machined parts.
The ratio of parts inspected will vary, but generally, due to the high repeatability of CNC machining, there is little need to do a large percentage sampling except for the most demanding applications.
Conclusion
The significance of surface roughness in CNC machining is vital as it influences the functionality, performance, aesthetic quality, and cost of machined parts. By selecting an optimal surface finish, manufacturers can enhance mechanical performance and visual appeal, optimizing component interactions in terms of movement and friction. Therefore, achieving the right balance of surface roughness is critical, necessitating a thorough understanding of material properties, design, and intended use to ensure reliability, cost-effectiveness, and customer satisfaction in manufacturing outputs.
Fig. 3: CNC Turned Components
Choose Komacut
If you are looking to achieve precise and tailored surface finishes for your CNC machining projects, exploring the services offered by Komacut is highly recommended. Komacut stands at the forefront of CNC machining services, combining advanced technology with deep industry expertise to meet your specific requirements.
At Komacut, we understand the critical role that surface roughness plays in the functionality and aesthetics of machined parts. Our team of experts uses state-of-the-art equipment and up-to-date techniques to deliver the exact surface finishes needed for your projects, ensuring optimal performance and quality.
Start your project with us today, and experience firsthand how our tailored machining solutions can enhance your products and streamline your manufacturing process. Visit our website to learn more or contact our team to discuss how we can assist you in achieving the desired outcomes for your next project.
Fig. 4: Quotation Process at Komacut
FAQs
What is surface roughness in CNC machining?
Surface roughness refers to the texture of a machined surface and is measured by the irregularities on the surface. It is quantified by the average height of the irregularities from a mean line over a specified distance, typically measured in micrometers or microinches.
Why is surface roughness important in CNC machining?
Surface roughness is critical because it can significantly affect the mechanical properties of a part, such as friction, wear resistance, and lubrication. Proper surface roughness ensures the part functions optimally in its application, whether it needs to move smoothly against another surface or seal tightly.
How is surface roughness measured?
Surface roughness is commonly measured using a profilometer, which traces a needle over the surface of the part and records the variations in surface height. The data collected is used to calculate the roughness average (Ra), which gives a numerical value indicating the smoothness of the surface.
What factors affect the choice of surface roughness in a project?
Several factors influence the choice of surface roughness, including the material being machined, the function of the part, the environment in which it will operate, and aesthetic considerations. Each factor must be carefully considered to select the most appropriate surface finish.
Can the desired surface roughness always be achieved?
While CNC machines are highly capable of achieving a wide range of surface finishes, the ultimate roughness achievable is influenced by the type of material, the condition of the machine, tool sharpness, and machining parameters such as speed, feed, and depth of cut. Sometimes, additional finishing processes may be required to achieve the desired smoothness.
How does surface roughness impact the cost of CNC machining?
Generally, achieving finer surface finishes requires more precise machining, additional passes, and so more machining time and cost. It's important to balance the need for a smoother surface with the cost implications to ensure economic feasibility.
What are some common mistakes when specifying surface roughness?
Common mistakes include over-specifying surface roughness, leading to unnecessary costs, or under-specifying, which can result in parts that do not perform adequately in their intended application. Clear communication and understanding of the functional needs of the part are crucial to avoid these issues.
What are the typical surface roughness values and what do they mean?
Surface roughness is typically measured in micrometers (µm) or microinches (µin), with common values ranging from as low as 0.025 µm (extremely smooth) to above 12.5 µm (relatively rough). Lower values are often required for high-precision applications such as aerospace components where surfaces must slide smoothly, while higher values may suffice for less critical applications like structural components.
How do different manufacturing processes affect surface roughness?
Different CNC machining operations, such as turning, milling, or grinding, produce different levels of surface roughness. For example, grinding can achieve very smooth finishes, while milling might leave a comparatively rougher surface. The choice of process depends on the part requirements and the desired final surface texture.
How do I choose the right surface roughness for my project?
Choosing the right surface roughness involves considering the functional requirements of the part, the material, the type of load it will bear (dynamic or static), and its exposure conditions (e.g., environmental elements). Consulting with a machining expert can also provide insights based on experience with similar parts and materials.